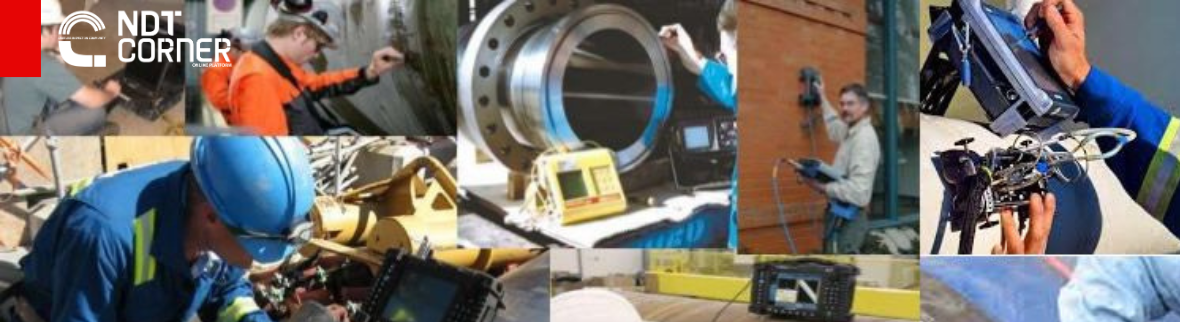
Top 10 Non-Destructive Testing Methods That Are Used Often
24 Nov 2022 Download PDF
Industries Where Non-Destructive Testing Is Used
NDT could be used in almost every industry type as visual inspections occur around every workplace. For better understanding, here are some industries listed below that use NDT:
-
Aerospace
-
Mining
-
Mineral
-
oil & gas
-
Chemical
-
Construction
-
Automotive
-
Biomedical devices
-
Primary metals
-
Marine
The 10 Most Widespread NDT Methods
There are various techniques used under NDT methods, with each having its own types of tools, data, & training. Few techniques enable detailed assessment of an element, and some of them simply allow for an exterior examination. Given below are the ten most often used Non-destructive methods:
1. Visual (VT)
2. Magnetic (MT)
3. Penetrant (PT)
4. Ultrasonic (UT)
5. Radiography (RT)
6. Eddy Current (ET)
7. Magnetic Flux Leakage (MFL)
8. Phased Array UT (PAUT)
9. Acoustic Emission (AE)
10. Electromagnetic Testing (ET)
Let's have a detailed study of these ten NDT methods.
1) Visual Testing (VT) is the most basic form of NDT testing. Technicians look at the equipment, material, or asset and notice flaws during visual inspections. They may also use a specialized device to handle a Remote Visual Inspection. Visual testing often provides an excellent place to start assessments, but you may require more in-depth assessments to get definitive results.
2) Magnetic Testing (MT) looking for the flaws in ferromagnetic materials by assessing any disruptions in the flow of their magnetic field. Inspectors perform these tests by inducing a magnetic field and introducing iron particles to the material’s surface. Inspectors observe the movement of the magnetic particles to look for imperfections. Assessing the magnetic field in this way allows technicians to check on the state of equipment without damaging the material. MT should not cause any health risks to inspectors.
3) Penetrant Testing (PT) indicate breaks or defects in the surface of pieces of equipment. Technicians perform liquid penetrant testing by applying a liquid that contains either a visible dye or a fluorescent dye to the surface of an object. The inspectors rub away excess liquid; any liquid that remains behind indicates a defect. Once crews notice the flaws, they examine them in greater detail with ultraviolet (UV) lights if they use a fluorescent dye. PT works very well to identify defects, and technicians can easily clean up after the process by washing away the dye.
4) Ultrasonic Testing (UT) use high-frequency sound waves during UT. They transmit the sound waves at the material or asset under inspection and look for any property changes. Many forms of UT use pulse echoes, which involve looking for surface imperfections based on the echoes reflected off of an item.
5) Radiographic Testing (RT) use radiation to complete RT. Often, crews use x-rays if they’re dealing with thin materials. However, they may choose gamma radiation instead if they need to assess a dense or thick material, requiring a thickness measurement before beginning the assessment. Experts use a variety of processes to report the results of RT. For example, they may use computed tomography, computed radiography, digital radiography.
6) Eddy Current NDT (ET) electromagnetic testing. This process allows crews to measure the magnetic field of a material based on its eddy currents (or electrical currents). Eddy current testing generally works best on non-ferrous materials. It used for surface and near surface cracks, used on metal, welds and tubes.
7) Magnetic Flux Leakage (MFL) testing utilizes a strong magnet, which creates a magnetic field that crews use when assessing structures made of steel. Use sensors to track any changes in the magnetic flux lines or density, which may indicate issues like: Pitting, Erosion, Corrosion. Monitoring the magnetic field allows crews to assess issues with large structures without causing any damage. Technicians often spend a significant amount of time studying magnetic field science and magnetic flux density before completing these tests.
8) Phased Array UT (PAUT) serves as a variation of traditional UT. This kind of test uses an array that can create independent pulses. Technicians control how each element fires, allowing them to steer or focus the sound beams. They can move the beam to various depths and angles, easily generating cross-section views of equipment or materials. Some examples of PAUT used a virtual probe to gather additional information in this NDT method.
9) Acoustic Emission Testing (AE) use to look for defects and imperfections with this NDT testing method. First, they monitor acoustic energy bursts, focusing on the location of the burst, its intensity, and its arrival time. Acoustic emission testing works well for companies operating in many different industries.
10) Electromagnetic - EC Tube Inspection is a key NDT practice in the Power Generation/Heat Exchanger sector and Eddy Current is one of the best methods of measuring wall thickness and circumferential cracks. Tubes may be inspected using ECT from the outer diameter (OD) at the time of manufacture and from the inner diameter (ID) for in-service inspection. Tube inspection equipment has a multi-channel to use different probes (ET, MFL, IRIS, RFT, NFT, and ECA). These all probes go inside the tube for Wall Loss, Corrosion, Cracks, etc. either (ID) or (OD) detection.