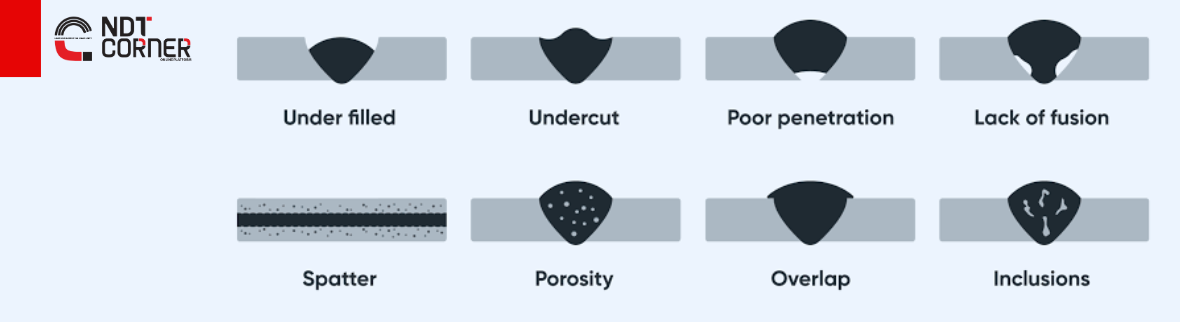
Welding Defects Types, Causes, Prevention
10 Oct 2023 Download PDF
Welding Defects
Welding defects are imperfections that occur during different welding processes. There are various reasons why welding defects occur during an operation.
Welding services are mainly used in the manufacturing industry for joining metals in constructing buildings, bridges, automobiles, aircraft, pipes, and many other objects. However, welding is not a perfect process as numerous types of welding defects can occur internally or externally in the welded metal.
Let’s explore some of the more common weld defects, their causes, and remedies.
Contents
1. What Is a Weld Defect?
2. External Welding Defects
3. Internal Welding Defects
4. Other Welding Defects
5. How to Detect Welding Defects
6. Conclusion
What Is a Weld Defect?
A weld defect results from a poor weld, weakening the joint. It is defined as the point beyond the acceptable tolerance in the welding process.
Imperfections may arise dimensionally, wherein the result is not up to standard. They may also take place in the form of discontinuity or in material properties. Common causes of welding defects come from incorrect welding patterns, material selection, skill, or machine settings, including welding speed, current, and voltage.
When a welded metal has a welding defect present, there are multiple options for resolving the issue. In some cases, the metal can be repaired, but at other times the metal itself has melted and the welding procedure needs to be restarted.
Weld irregularities occur for a variety of reasons and it results in different welding defects. They can be classified into two major categories: internal welding defects and external welding defects.
External Welding Defects
External welding defects refer to discontinuities in the weld metal that are noticeable to the naked eye.
Cracks
Cracks are the worst welding defect since they can rapidly progress to larger ones, which inevitably leads to failure. Weld cracks are mainly classified depending on how they form in the weld bead.
Longitudinal cracks form parallel to the weld bead while transverse cracks form across the width. Crater cracks form at the end of the bead, where the arc concludes.
Welding cracks can also appear at varying temperatures:
-
Hot cracks form when weld joints crystallise as the parent and base metals are heated above 10000°C. The primary reasons for hot cracks is when an incorrect filler metal is used and when the workpieces undergo high heating and cooling rates in processes such as laser welding.
-
Cold cracks form after the cooling process of the weld metal. The weld crack may form hours or days after the metal’s cooling process.
Causes
-
Using hydrogen shielding gas in welding ferrous metals.
-
Ductile base metal and the application of residual stress.
-
Rigid joints that constrain the expansion and contraction of the metal.
-
Use of high levels of sulphur and carbon.
Prevention
-
Preheating the metals and gradually cooling the weld joints.
-
Maintaining acceptable weld joint gaps.
-
Selection of the correct welding materials.
Porosity
Porosity is the formation of holes in the weld pool resulting from gas bubbles that cannot escape. It is usually one of the common welding defects when using shielding gas, which is present in welding techniques such as TIG and stick welding. Absence, lack, or too much shielding gas may lead to metal contamination, which reduces the strength of the weld.
On the other hand, severe versions of porosity come in the form of blow holes or pits when large gas bubbles get trapped in the weld pool. Additionally, smaller gas molecules can blend with the weld metal, forming an impure compound.
Causes
-
Unclean welding surface.
-
Wrong electrode selection.
-
Lack or absence of shielding gas.
-
Mishandled or damaged shielding gas cylinder.
-
Either too low or too high welding current.
-
Fast travel speed.
Prevention
-
Cleaning the weld surface.
-
Using the correct welding electrode.
-
Preheating the metals before welding.
-
Proper gas flow rate setting to achieve the right amount of shielding.
-
Regularly checking for moisture contamination in the shielding gas cylinder.
-
Adjustment of welding current and travel speed settings.
Undercut
An undercut can be formed in various ways but mainly it is tied to two reasons. The first is using excessive current – the edges of the joint melt and drain into the weld. The second reason is not that enough filler metal is deposited into the weld. This results in a reduced cross-section meaning that there are notches or grooves along the weld, which increase stress when the material is subjected to fatigue loading. This defect occurs at the toe of the weld or in the case of multi-run welds, in the fusion face. An undercut may come from continuous, intermediate, and inter-run.
Additionally, water and dirt are prone to get stuck into the groove and this can accelerate corrosion in the already weakened area.
Causes
-
High arc voltage.
-
Incorrect electrode selection or wrong electrode angle.
-
High travel speed.
Prevention
-
Smaller arc length, voltage, and travel speed.
-
30 to 45-degree electrode angle.
-
Reducing the electrode diameter.
Overlap
Overlap is the excess metal that spreads out around the bead. The spread-out filler metal is not properly mixed with the base metals. Typically, it comes in a round shape over the weld joint.
Causes
-
Incorrect welding procedure.
-
Wrong selection of welding materials.
-
Improper preparation of base metals.
Prevention
-
Smaller welding current.
-
Use of proper welding techniques.
-
Shorter welding electrode.
Burn-Through
An open hole is exposed when the welding process accidentally penetrates the whole thickness of the base metal, creating a burn-through or melt-through. This is one of the common weld defects when welding thin metals.
Causes
-
High welding current.
-
Extreme gap to the root.
-
Not enough root face metal.
Prevention
-
Maintaining a proper root gap.
-
Control in the application of welding current.
-
It can be repaired in some cases wherein the hole is removed and re-welded.
Spatter
Spatter is a welding defect that occurs when metal droplets are discharged on the metal surface. It solidifies and becomes stuck on the metal surface once it cools down. In most cases, spatter does not alter the structural integrity of the weld but generally, it has to be removed, adding to the total costs.
Causes
-
High arc length.
-
High welding current.
-
Improper shielding of the heat-affected zone.
-
Using the wrong polarity may create excessive spatter.
Prevention
-
Choosing the correct weld polarity.
-
Selecting a better shielding gas and better shielding technique.
-
Reducing the welding current and arc length to optimal condition.
Under Filled
Underfill occurs when too little weld metal is deposited into the joint. As a result, some of the parent material remains unfused and the joint is under filled. These unfused sections, even when small, act as potential stress raisers.
Causes
-
Low welding current.
-
Too high travel speeds.
- Incorrect weld bead placement.
-
Laying weld beads too thinly in multi-pass welds.
Prevention
- Proper electrode size selection.
-
Selecting the right current setting.
-
Avoid moving too fast.
Excess Reinforcement
Excess reinforcement (overfilled) describes a weld that has too much build-up. It is the opposite of underfilled welds as excessive amounts of filler metal is deposited into the joint. With this defect, high levels of stress concentration build up in the toes of the welds.
Causes
-
Low travel speeds.
-
Incorrect procedures.
- Excess flux on the feed wire.
Prevention
-
Maintaining an optimal pace with the torch.
-
Avoiding excess heat by making sure to use the correct voltage and amperage.
-
Aligning the workpieces properly to ensure that the gap between the parts is not too large.
Mechanical Damage
Mechanical damage is indentations present in the weld due to damage from preparation, handling, welding, equipment usage, and other factors.
Causes
-
Unnecessary application of external force before, during, or after an operation.
-
Incorrect handling of welding equipment
-
Not engaging the arc before the welding procedure
Prevention
-
Safe and correct handling of welding equipment.
-
Consistently engaging the arc in the metal parts before starting welding.
Distortion
Distortion or warping is an accidental change in the shape of the surrounding metal of the weld. Excessive heating around the weld joint is the main reason for distortion around its area.
Warpage or distortion mostly occurs in thin metals and is classified into four types: angular, longitudinal, fillet, and neutral axis.
Causes
-
Thin weld metal.
-
Incompatible base metal and weld metal.
-
High amount of weld passes.
Prevention
-
Using suitable weld metals.
-
Optimising the number of weld passes.
-
Selection of better welding methods for the metal type.
Misalignment
Improper positioning of metals before or during a welding operation may result in misalignment. Poor metal alignment is susceptible to fatigue conditions especially if it is used in pipe welding.
Causes
-
Rapid welding process.
-
Incorrect metal alignment or metals aren’t secured properly.
-
Lack of welder skills.
Prevention
-
Employing a slower and more stable welding procedure.
-
Securing the metals firmly before and during operation.
-
Using the correct welding techniques and conducting checks regularly.
Internal Welding Defects
Welding processes that create weld defects invisible to the naked eye are categorised as internal welding defects.
Slag Inclusion
A weld bead that contains slag in its composition compromises the toughness and structure of the metal. Slag inclusion may occur either on just the surface of the weld metal or in between welding cycles. This weld defect is common to processes that use flux, such as stick, flux-cored, submerged arc welding, and brazing.
Causes
-
Incorrect welding angle and travel speed of the welding torch.
-
Poor pre-cleaning of the edge of the weld surface.
-
Low welding current density resulting in inadequate heating of the metals.
Prevention
-
Higher welding current density.
-
Optimal welding angle and travel speed to avoid slag inclusion in the weld pool.
-
Consistent weld edge cleaning and slag removal of each layer.
Incomplete Fusion
Incomplete fusion results from poor welding wherein the metals pre-solidify, forming gaps in the weld zone. When the welder cannot properly melt the parent metal with the base metal, it results in a lack of fusion.
Causes
-
Low heat input resulting in metals not melting.
-
Wrong joint angle, torch angle, and bead position.
-
Extremely large weld pool.
Prevention
-
Higher welding current and slower travel rate to ensure the melting process of the metals.
-
Improving welding positions such as joint angle, torch angle, and bead position.
-
Lower deposition rate.
Incomplete Penetration
Incomplete penetration generally occurs during butt welding, wherein the gap between the metals isn’t filled completely through the joint thickness. This means that one side of the joint is not fused in the root.
-
Incorrect use of the welding technique.
-
Wrong electrode size.
-
Low deposition rate.
Prevention
-
Using the correct welding technique and procedure.
-
Higher deposition rate.
-
Proper electrode size selection.
Other Welding Defects
Whiskers
Whiskers are a specific weld defect in the MIG welding process. This occurs when the root side of a weld joint has remnants of the wire electrode.
Causes
-
The electrode is positioned ahead of the leading edge of the weld puddles.
-
Fast wire feed speed of the electrode wire to the MIG torch.
-
High travel speed while welding
Prevention
-
Snipping off the small blob of the electrode before welding
-
Reducing the wire feed speed in the machine settings.
-
Slowing down the travel speed or using welding techniques as countermeasures, such as whipping the electrode.
Necklace Cracking
Necklace cracking is a welding defect associated with electron beam welding. This defect occurs when the molten metal can’t sufficiently flow into the cavity, resulting in incomplete penetration.
Causes
-
Using metals such as stainless steel, carbon steel, tin, and nickel-based alloys.
-
Improper welding technique application.
-
High operation speed in electron beam welding.
Prevention
-
Better material selection for electron beam welding.
-
Using constant speed to achieve uniformity.
-
Applying proper welding technique and procedure.
How to Detect Welding Defects
Testing methods are a great way to check if the welding patterns meet specific criteria. It allows us to find the causes and remedies for why welding defects occur. While it takes some time, it ensures that the welds are safe and risk-free.
There are two standard procedures for finding defects in a weld metal:
Non-Destructive Testing
Non-destructive testing allows us to observe discontinuities in the weld incurring no damage. This testing method is essential in high-speed production wherein a sample is tested from a batch.
Non-destructive testing and evaluation is usually done by utilising visual inspection, liquid penetrants, magnetic particles, eddy currents, ultrasonics, acoustics, emissions or radiography.
Destructive Testing
Destructive testing acquires information by subjecting the finished projects to strenuous methods until it reaches their limits. Some cases require destructive testing in addition to non-destructive tests in order to reduce weld defects in production significantly.
Some destructive methods used to identify the limits of the weld metal are acid etch, guided bend, free bend, back bend, nick break, and tensile strength.
Conclusion
Welding defects pose serious risks that can lead to dangerous issues if not addressed. They can be expensive and time-consuming to correct but are always worth it in exchange for quality. This is why welders need to understand the fundamentals of welding.
Modern technology allows us to perform welding techniques more efficiently. Along with numerous testing methods facilitating the discovery of different types of welding defects, the execution and correction of these imperfections is constantly getting better. Focusing on improving both the machinery and technical skill make up a difference when it comes to limiting weld defects. This leads many industries to manufacture products of higher quality than ever before.